- A+
作为一种新型金属材料,中熵合金(MEA)由于其优异的性能,包括优异的强度和延展性、高断裂韧性、抗冲击性和耐磨性等,近年来引起了广泛的研究兴趣。对MEA中原子尺度机制的研究已将优异性能与多种变形机制联系起来(包括粗略位错滑移、大量部分位错和层错生成、纳米孪晶及其协同作用)。多主元素合金中不可避免的化学短程有序和严重的晶格畸变被认为是导致其性能优异的原因。面心立方(FCC)晶体结构的CoCrNi MEA是MEA中最具代表性的体系。CoCrNi MEA具有约1 GPa的超高极限强度、约70%的破坏应变和室温下超过200 MPa m1/2的KIC断裂韧性。虽然CoCrNi MEA的力学性能已被广泛研究,但其更复杂的力学行为还未被探索,如摩擦和磨损。调整CoCrNi MEA的摩擦学性能非常重要,因为它限制了该材料的长期使用以及强度和延展性。纳米划痕测试可以广泛深入了解纳米尺度下材料的塑性变形机制,并广泛用于研究各种材料的纳米结构行为和摩擦/磨损性能,包括合金、金属玻璃和陶瓷材料。而分子动力学模拟是研究金属纳米核塑性机制的首选技术。因此,来自西北工业大学的Wan Wang等人使用分子动力学方法研究了CoCrNi MEA的纳米开裂变形机制。纳米划痕模拟的CoCrNi MEA模型如图1所示,它由FCC CoCrNi MEA样品和半径为30 Å的虚拟球形压头组成。模型尺寸为126 Å×105 Å×140 Å,对应的晶向分别为X-[–110], Y-[111]和Z-[11–2]。模拟过程分为两个阶段,即纳米压痕和纳米划痕。在第一阶段,压头以10 m/s的速度向-Y方向压入2 nm。在第二阶段,压头以2 nm的压入深度和10 m/s的滑动速度沿X方向运动。
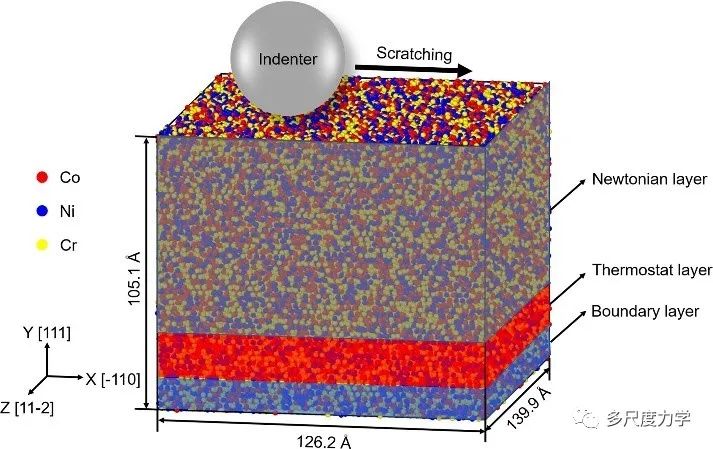
图2显示了CoCrNi MEA和纯Ni在划痕过程中的摩擦学性能曲线。这些曲线可分为从压痕到划痕的过渡阶段和稳定划痕阶段。横向力和法向力的变化主要由划痕阶段的波动决定。这些曲线根据位错演化分为三个阶段:过渡阶段、第一划痕阶段和第二划痕阶段。在过渡阶段,系统从纳米压痕转变为纳米破裂模式。压头的后部逐渐与基体脱离接触,导致横向力增加,法向力急剧减小。在第2阶段,横向力(摩擦力)Fτ未饱和,但由于刮痕尖端前方形成的正面堆积,如图2(a)所示,而法向力Fn相对稳定,如图2中(b)所示。然而,在第3阶段,CoCrNi MEA的摩擦力和法向力的下降明显,这标志着位错的突然大规模增加。
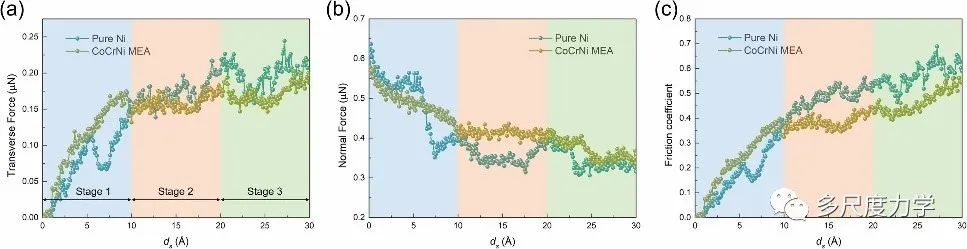
根据图3(a)和(b)所示的位错分布,可以发现,压头周围的位错大大减少。大量Shockley不全位错积累在压痕区,然后随着尖端开始划痕,在自由表面上滑动并湮灭。在第2阶段,Shockley不全位错的稳定增长导致纯Ni中的摩擦曲线相对稳定。图4(c)显示,不全位错主要产生于压头前方,并快速滑入晶体。如图4(c)至(d)所示,位错的湮灭发生在划痕槽的中间,并且位错的累积位于划痕的前沿。此外,由于纯镍中的不全位错很容易从压头中滑出,因此不同滑移面中的不全位错在压头下方发生反应的可能性很小。因此,在纳米刮痕过程中,不可动位错的长度保持在较低的水平。
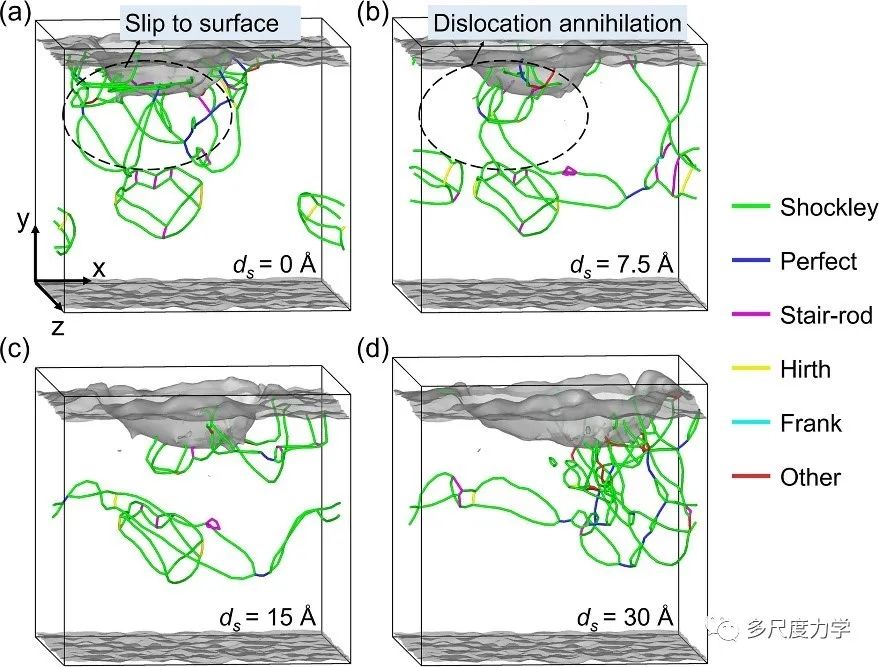
相比之下,MEA的位错长度变化(图4)与纯镍的完全不同。在阶段1,CoCrNi的纳米刮痕过程中形成了一个独立的棱柱位错环(PDL),除了PDL外,几乎没有位错可以从压头滑出并向下扩展到底部,如图4(a)至(c)所示。在第2阶段,位错湮没发生,导致位错长度大规模减小,如图4(c)至(d)所示。在第三阶段,越来越多的原子堆积在划痕前沿,导致摩擦力增加,而肖克利不全位错的雪崩导致法向载荷下降。位错的增加将迅速填充压头前方的塑性区,达到所需的位错密度,以维持塑性划痕。此外,塑性区内不全位错的高密度将导致广泛的相互作用和阶梯杆位错的形成(见图4(e)和(f))。阶梯杆锁数量的增加会严重阻碍错位运动,并起到加强作用,这也是摩擦力增加的原因之一。
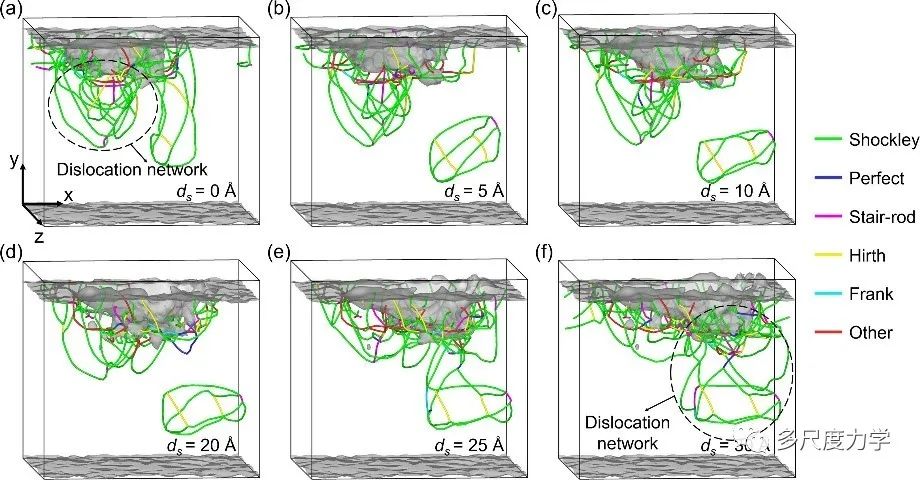
为了解释纯Ni和CoCrNi MEA中两种不同的位错演化,计算了广义层错能(GSFE),并比较了Shockley不全位错和全位错的长度,如图5所示。CoCrNi MEA中Shockley不全位错的长度明显高于纯Ni(见图5(b)),这与CoCrNi的低层错能有关(见图5(a))。由于CoCrNi MEA化学复杂性,MEA中的Shockley不全位错可以被局部结构势垒显著钉住,而Ni中的Shokley不全位错可以快速自由地滑动。由于成核速率高,但运动迟缓,CoCrNi MEA中的不全位错容易交叉纠缠,并通过位错反应形成阶梯杆位错和Hirth位错锁。因此,对于CoCrNi MEA来说,大多数位错被限制在塑性划痕区内。相比之下,纯镍中的位错很容易滑移,晶格摩擦力较低,因此更多的位错可以向下滑移。此外,纯镍具有更高的层错能量,因此在划痕过程中会产生更多的全位错。

纯Ni和CoCrNi MEA的表面原子堆积形态及高度如图6所示。表面堆积形态显示出明显的不对称性(见图6(a))。图6(b)显示了划痕末端CoCrNi MEA划痕表面的俯视图。大量原子聚集在压头前面和划痕槽两侧, 各向同性表面堆积是CoCrNi中位错运动缓慢的结果,这与压头周围形成的更稳定塑性区有关。因此,密集位错被限制在划痕槽周围,导致均匀塑性变形和表面堆积。在纳米划痕模拟过程中,磨损率(或磨损碎片的百分比)定义为构成表面上堆积的原子与基底总原子的比率。图6(c)显示了CoCrNi MEA和纯Ni的最大堆积高度和磨屑数量百分比。纯Ni的最大堆积高度和磨屑数量百分比高于CoCrNi MEA,表明CoCrNi具有更好的耐磨性。
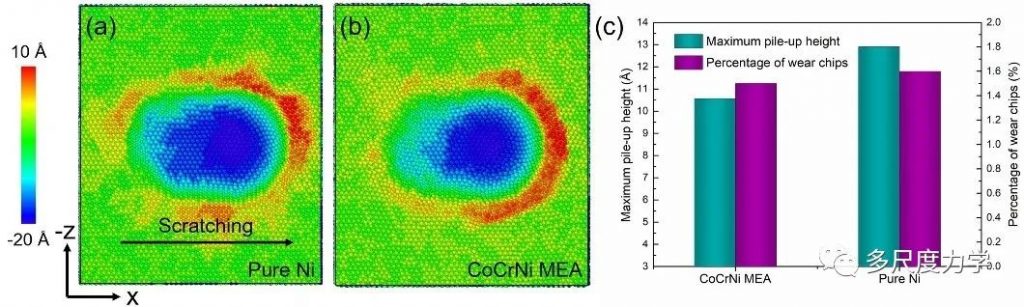
在CoCrNi MEA的纳米裂纹形成过程中产生了一些纯Ni中不存在的典型缺陷结构。为了对此提出合理的解释,分析了压头下方的横截面剪切应力分量τxy,τxy的分布如图7所示。局部横截面区域的剪切应力可分为压缩区(红色区)和拉伸区(蓝色区)。图6(a)中所示的一对平行堆叠断层形成于两个不全位错之后,位错沿着滑块方向,由压头前方的压力驱动。棱柱形位错环(PDL)的形成和运动也与压应力场密切相关。然而,在球面接触的后部,剪切应力逐渐从压缩转变为拉伸,从而将先前推入工件的位错再次拉回到表面,这可以解释压头经过后Ni中位错的消失。拉应力促进了划痕压头后面不全位错的形核,这导致了摩擦诱发的微观结构的形成,如孪生和相变。
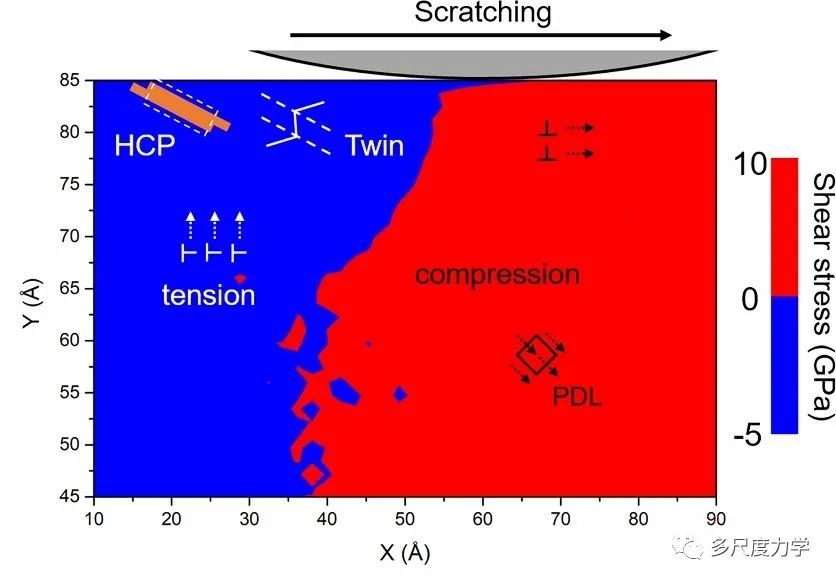
在划痕槽后面观察到了从FCC到HCP的相变过程。拉伸应力场促进不全位错形核,这为CoCrNi MEA的相变和孪晶变形奠定了基础。在SF3缓慢传播过程中,一个新的不全位错在附近的晶面上形核,从而形成SF4。随着SF4的不断膨胀(见图8(b)和(c)),FCC结构的堆叠顺序发生了变化,形成了HCP带。变形过程中的相变有助于提高材料强度和延展性。
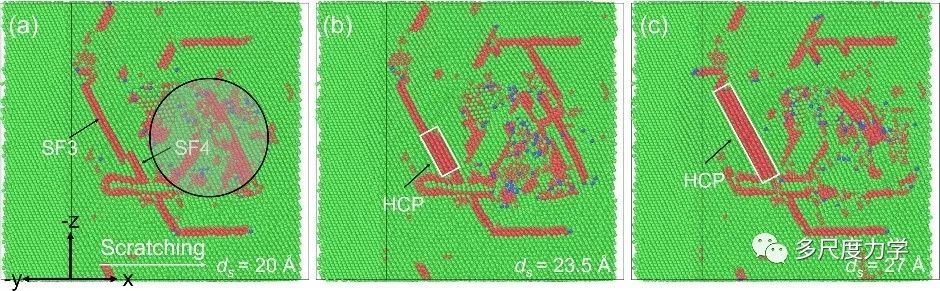
如图15所示,在划痕槽后面还观察到孪晶变形。在晶体中,不全位错沿着滑移系滑动,留下了内层错。然后,通过内层错的相邻晶面上的不全位错的连续滑动,形成了双层孪晶。图9(a)显示了CoCrNi MEA中ds=1 nm处划痕槽后面形成的双层孪晶。图9(b)是双层孪晶结构Z-Y横截面。两层孪晶出现在划痕槽表面附近的区域,由压头后面的拉伸应力促进。形成的两层孪晶在阻碍后续位错的移动方面起着主要作用,有助于增强效应。
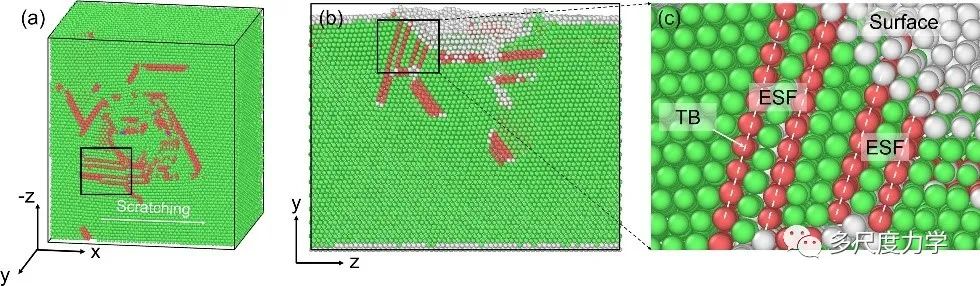
相关研究成果以“Molecular dynamics simulation of deformation mechanism of CoCrNi medium entropy alloy during nanoscratching”为题发表在Computational Materials Science(Volume:203,2022,111085)上,作者为WanWang等人。
